Mechanical engineering
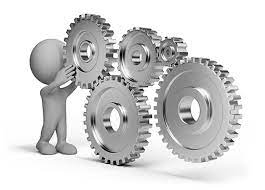
ABOUT THE DEPARTMENT
Mechanical engineering emerged as a field during the industrial revolution in Europe in the 18th century; however, its development can be traced back several thousand years around the world. Mechanical engineering science emerged in the 19th century as a result of developments in the field of physics. The field has continually evolved to incorporate advancements in technology, and mechanical engineers today are pursuing developments in such fields as composites, mechatronics, and nanotechnology. Today we found on the globe the majority of technical works are carried by Mechanical Engineering irrespective of the type of work. Mechanical engineering overlaps with aerospace engineering, metallurgical engineering, civil engineering, electrical engineering, petroleum engineering, manufacturing engineering, chemical engineering, and other engineering disciplines to varying amounts. Mechanical engineers may also work in the field of Biomedical engineering, specifically with biomechanics, transport phenomena, biomechatronics, bionanotechnology and modeling of biological systems, like soft tissue mechanics. Since most of the works carried out by Mechanical graduates the demand for this branch has increased in the market since its inception.
About | Academics | Funded Projects | Workshops & Seminars | Alumni | Testimonials | Contact
About the Department
VISION
To provide world-class facilities for education and research in Mechanical Engineering to meet the changing needs of the society.
MISSION
• To prepare effective and responsible graduate and post graduate engineers for global requirements by providing quality education
• Respond effectively to the needs of the industry and changing world.
• Conduct basic and applied research and to generate intellectual property
• Provide consultancy to the neighborhood and cultivate the spirit of entrepreneurship
Program Educational Objectives (PEOs)
• Graduates will achieve successful professional career in IT industry with the approach of lifelong learning.
• Graduates will possess technical competency to design develop and solve engineering problems related to IT industry.
• Graduates will attain the qualities of professional leadership to deliver effectively in multidisciplinary global working environment with professionalism and ethical values
Program Outcomes (POs)
• Engineering Knowledge Apply the knowledge of mathematics, science, engineering Fundamentals, and an engineering specialization to the solution of complex engineering problems.
• Problem Analysis: Identify, formulate, review research literature, and analyze complex engineering problems reaching substantiated conclusions using first principles of mathematics, natural sciences, and engineering sciences.
• Design/ Development of Solutions: Design solutions for complex engineering problems and design system components or processes that meet the specified needs with appropriate consideration for the public health and safety, and the cultural, societal, and environmental considerations.
• Conduct Investigations of Complex Problems: Use research-based knowledge and research design of experiments, analysis and interpretation of data, and synthesis of the information to provide valid conclusions.
• Modern Tool Usage: Create, select, and apply appropriate techniques, resources, and modern engineering and IT tools including prediction and modeling to complex engineering activities with an understanding of the limitations.
• The Engineer and Society: Apply reasoning informed by the contextual knowledge to assess societal, health, safety, legal and cultural issues and the consequent responsibilities relevant to the professional engineering practice.
• Environment and Sustainability:Understand the impact of the professional engineering solutions in societal and environmental contexts, and demonstrate the knowledge of, and need for sustainable development.
• Ethics: Apply ethical principles and commit to professional ethics and responsibilities and norms of the engineering practice.
• Individual and Team Work: Function effectively as an individual, and as a member or leader in diverse teams, and in multidisciplinary settings.
• Communication: Communicate effectively on complex engineering activities with the engineering community and with society at large, such as, being able to comprehend and write effective reports and design documentation, make effective presentations, and give and receive clear instructions.
• Project Management and Finance: Demonstrate knowledge and understanding of the engineering and management principles and apply these to one’s own work, as a member and leader in a team, to manage projects and in multidisciplinary environments.
• Life-long learning: To recognize the need for, and have the preparation and ability to engage in independent and life-long learning in the broadest context of technological change.
Program Specific Outcomes (PSOs)
• To provide students with a sound foundation in mathematical, scientific and engineering areas necessary to achieve excellence in solving and analyzing engineering problems and to prepare them for higher studies.
• To develop the ability among students to synthesize data and technical concepts for application to mechanical engineering tools.
• To motivate students to participate in multi- disciplinary projects.
• To prepare students for successful careers in industry that meets the needs of Industries/society and the country
• To promote and develop among the students an ambition of life-long learning and to apply them to professional ethics and codes of professional practices.
QUALITY POLICY
To produce the quality engineers to meet the industrial challenges globally
HOD's Message
Why Mechanical Engineering
SWOT
Strengths
• Wide-ranging and multidisciplinary research
• Teams able to implement test environments
• Strong process expertise and systemic thinking
• Good industry cooperation and networks, good ability to react to new research needs
• One Centre of Excellence, one Strategic Centre for Science, Technology & Innovation and several doctoral programmes in the field
Weakness
• Inadequate culture of publishing research results
• Weak researcher mobility and other exposure
• Early stages of research career hampered by insufficient supply of dissertation opportunities
• Undersized volume of doctoral programmes
• Underutilisation of funding opportunities offered by EU and other international mobility programmes
Opportunities
• Creating critical mass and increasing exposure through concurrent effects of Academy of Finland, Tekes and EU funding
• Utilising the ability to react swiftly in research into emerging topics and needs
• Increasing international research collaboration
• Stepping up cooperation with the BRIC countries (Brazil, Russia, India and China)
• More university agreements on collaboration
Threats
• Loss of production chains decreasing the number of research topics
• Culture trumps technology among young people, makes student recruitment more difficult
• Ever tighter budgets due to economic uncertainty
• Funding directed at standing themes
• Research fields trimmed based on performance indicators